Meltblown nonwoven fabric is used for various products like face masks, wipes, filters and insulation due to its very fine fiber structure and high surface area. Meltblown machines transform polymer resins into nonwoven webs through a process that “blasts” thin fibers onto a collector. Here are details on how these machines work:
What is A Meltblown Machine?
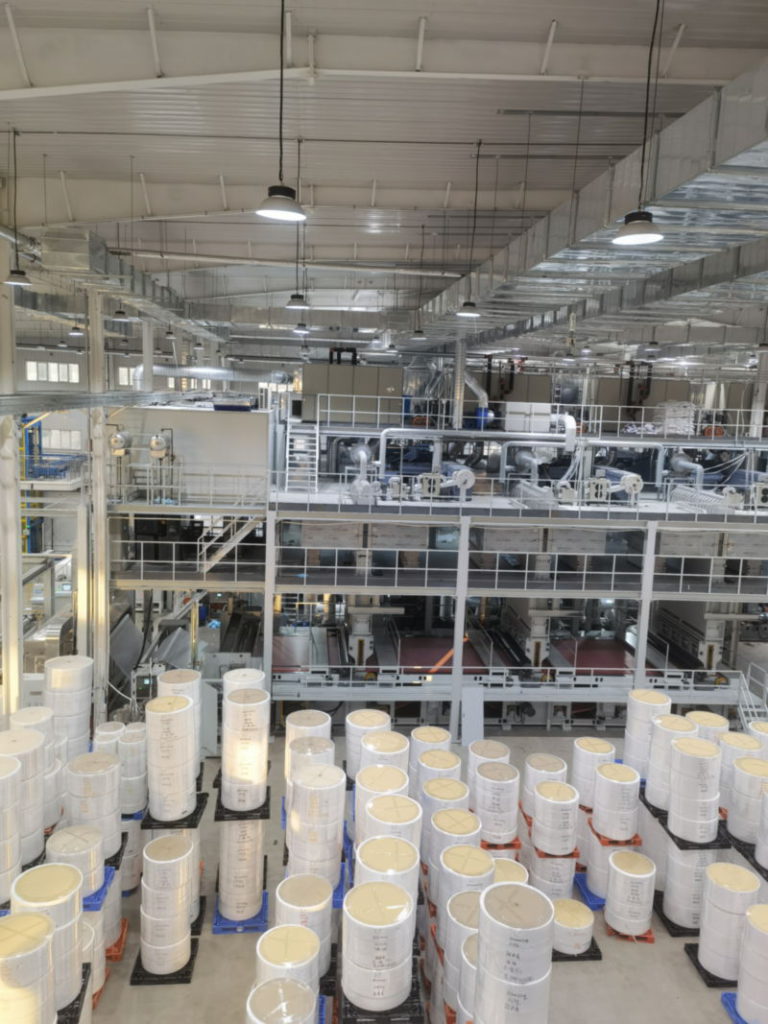
A meltblown machine uses extrusion and high-velocity air to produce nonwoven webs of meltblown fibers. The main components of the machine are:
- Extruder – Melts and pumps the polymer resin to the die assembly.
- Die Assembly – Contains multiple tiny nozzles or melt channels that extrude the molten polymer.
- Hot Air Supply – Blows high-temperature air across the exit of the nozzles.
- Conveyor Belt – Collects the extruded fibers to form a nonwoven web.
- Post-Treatment Unit – Includes web drawing, cooling, bonding and winding equipment.
In operation, the molten polymer is extruded through the die nozzles while high-temperature air flows across the nozzle exits. The airstream “blasts” and attenuates the extruding polymer into very fine fibers (0.5 – 50 μm).
The randomly dispersed meltblown fibers are then deposited onto the moving conveyor belt, which draws the web at the same rate that fibers are being laid down. As the web passes through the post-treatment unit, it is bonded, cooled and wound onto a reel.
How Meltblown Fibers Are Formed
The key to meltblown fiber formation is the high-velocity air that exits the die along with the extruding polymer. As the molten resin emerges from the nozzles, the airstream:
- Stretches the extruding polymer filaments very rapidly.
- Attenuates the filaments into fine fibers within 0.2 to 2cm of the die exit.
- Randomizes the fiber trajectories, causing them to distribute uniformly across the web.
The high air temperatures also help quench and solidify the meltblown fibers almost immediately after formation. This “traps” their fine fiber structure before fibers can recombine.
Features Of Meltblown Machines
Meltblown machines are characterized by:
- Die geometry – Slot, circular or rectangular nozzles with varying dimensions.
- Air flow – Air temperature, pressure and velocity.
- Throughput rate – How fast the machine converts resin into nonwoven fabric.
- Web characteristics – Basis weight, thickness, fiber diameter and pore size.
- Line width – The maximum nonwoven web width the machine can produce.
- Processing capacities – What polymer types the machine is optimized to process.
Manufacturers offer meltblown machines with different configurations, throughputs, and heating/cooling systems to produce a wide range of nonwoven web properties for various end uses.