أحدثت خطوط إنتاج الأقمشة غير المنسوجة PP ثورة في تصنيع الأقمشة غير المنسوجة, تقديم كفاءة محسنة, تحسين جودة المنتج, والتنوع. من خلال فهم تعقيدات خطوط الإنتاج هذه والاستفادة من مزاياها, manufacturers can meet the growing demand for high-quality nonwoven fabrics across various industries. The lightweight, breathable, customizable, and sustainable nature of PP spunbond nonwoven fabrics has positioned them as a preferred choice for applications ranging from hygiene products and agriculture to geotextiles and packaging.
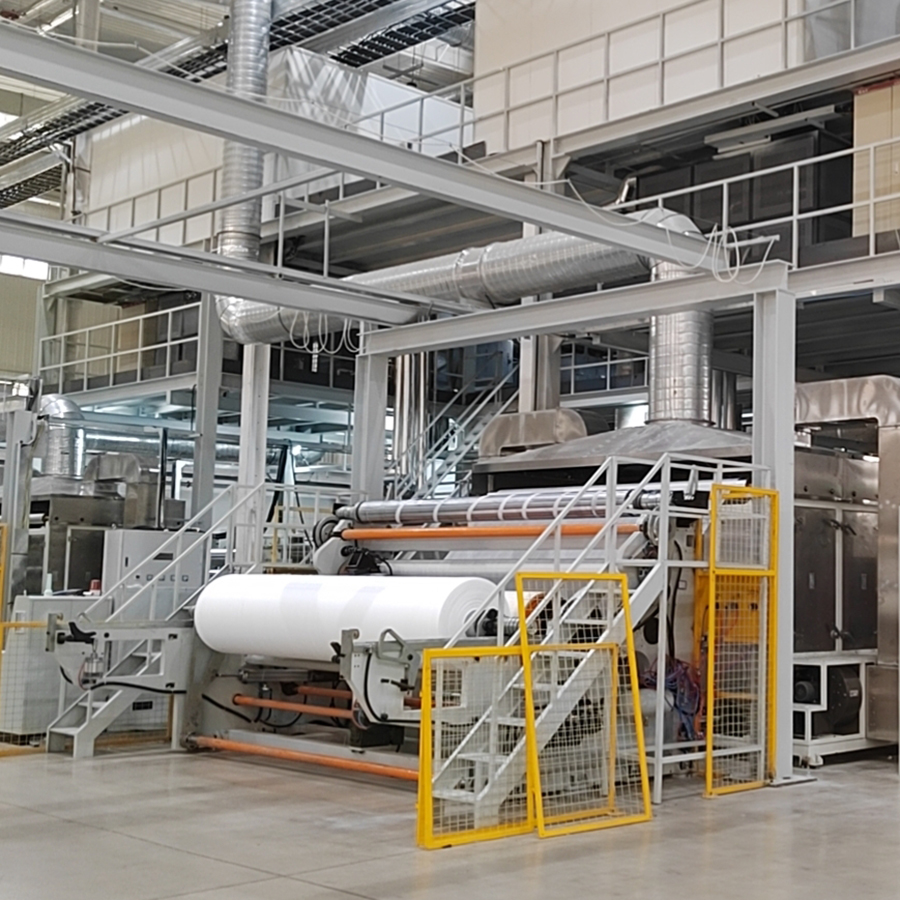
Understanding the PP Spunbond Nonwoven Production Process (Approx. 300 words):
The PP spunbond nonwoven production process involves transforming polypropylene (ص) granules into a continuous web of fibers, which are then bonded together to form a fabric. The production line consists of several key stages, each contributing to the final product’s quality and characteristics. Let’s explore these stages:
أ. Polymer Extrusion: The process begins with the extrusion of PP granules through a specialized extruder. The extruder melts the PP granules, forming a molten polymer melt.
ب. Filament Spinning: The molten polymer is then forced through spinnerets, which contain numerous tiny holes. As the polymer passes through these holes, it solidifies into fine filaments.
c. Web Formation: The filaments are collected onto a moving belt or conveyor to form a web. This web is initially in a loose and fragile state.
d. Web Bonding: To strengthen the web and impart the desired properties, the nonwoven fabric undergoes a bonding process. This can be achieved through various methods, including thermal bonding, chemical bonding, or mechanical bonding, depending on the desired characteristics of the final product.
e. Finishing and Winding: After bonding, the fabric goes through finishing processes such as calendaring or embossing to enhance its surface properties. The finished fabric is then wound onto rolls for further processing or distribution.
The Role of PP Spunbond Nonwoven Production Lines
PP spunbond nonwoven production lines by pp spunbond nonwoven production line supplier, play a pivotal role in optimizing the manufacturing process and ensuring the production of high-quality fabrics. Let’s explore the key components and advantages of these production lines:
أ. Extrusion System: The extrusion system consists of an extruder, melt pump, and spinneret. It is responsible for melting and filtering the PP granules, maintaining a consistent melt flow, and shaping the filaments through the spinnerets. Advanced extrusion systems offer precise control over parameters such as temperature, pressure, and melt quality, ensuring uniform filament formation.
ب. Web Formation and Laying: The web formation stage, often facilitated by a conveyor belt or forming drum, is critical for achieving uniformity in web width, weight, and thickness. Advanced production lines incorporate precise tension control systems and servo-driven components to ensure optimal web formation.
c. Bonding Techniques: PP spunbond nonwoven production lines accommodate different bonding techniques, allowing manufacturers to customize the fabric’s properties. Thermal bonding, which utilizes heated calender rolls or hot air, offers excellent strength and stability. Chemical bonding involves the application of binders to the web, providing specific characteristics such as softness or water resistance. Mechanical bonding techniques, such as needle punching or hydroentanglement, enhance fabric strength by mechanically interlocking the fibers.