From medical masks to air and liquid filtration media, melt blown nonwoven fabrics play a crucial role in modern industries and our daily lives. These specialized fabrics are produced through an advanced process utilizing melt blown fabric machines. Let’s explore the inner workings of this sophisticated technology.
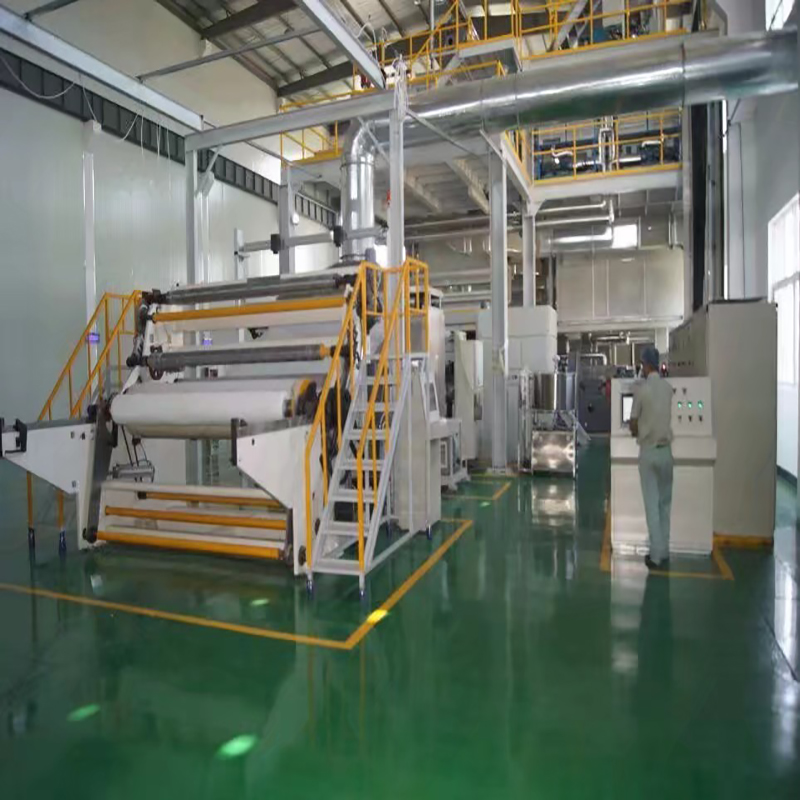
How It Works
In a melt blowing machine, polymer pellets (usually polypropylene or polyester) are continuously fed into an extruder barrel and heated to melt. The extrudate emerges through fine diameter spinneret die openings which divide it into filaments. High-speed heated air blows these filaments through attenuated air flows, stretching and thinning them as they are deposited in a collected web on a conveyor belt.
Key Components
Extruder melts and pumps polymer through the die head assembly. Temperature must remain precisely controlled.
Spinneret die plates contain thousands of micro-sized openings to divide the stream into fine filaments. Plate designs vary hole sizes and patterns.
Heated air guns directed at the filaments use air pressures from 100-500 PSI and temperatures from 200-400°F to draw out filaments.
Collection belt gathers deposited filaments into a nonwoven web which proceeds through heating/cooling rolls.
Fabric Properties
Filament diameters ranging from 0.5-10 microns yield high surface area webs from a few GSM up to several hundred. Fiber entanglement provides good strength while porosity and pore size distribution impart desired properties for filtration or PPE use. Machines precisely modulate fiber deposition parameters and web handling for consistent quality.
Filtration Applications
Common melt blown fabrics serve in masks, respirators, industrial and HVAC air filters, vacuum cleaner and engine air filters, oil filters and more. Through efficient depth loading and small pore structures, they effectively capture particles or liquids via various mechanisms down to sub-micron levels.
Quality Factors
Manufacturers evaluate web uniformity, thickness variation, particle/liquid filtration efficiencies and mechanical properties to ensure product suitability. Proper spinneret design, temperature controls, air velocity profiles and collection all influence outcomes requiring sophistication. Regular audits maintain optimized performance.
إجمالي, melt blowing utilizes precisely engineered thermoplastic processing and fiber formation methods delivering specialized nonwoven fabrics with diverse application ranges through consistent fine fiber production. Their crucial filtration roles rely on high-quality machine output.