لقد اكتسب القماش المنفوخ الذائب اهتمامًا كبيرًا في السنوات الأخيرة, خاصة بسبب دورها الحاسم في إنتاج مواد ترشيح عالية الجودة, الإمدادات الطبية والتطبيقات الأخرى المختلفة. This unique nonwoven fabric is created using a specialized process that involves melting polymer pellets and forming fine fibers.
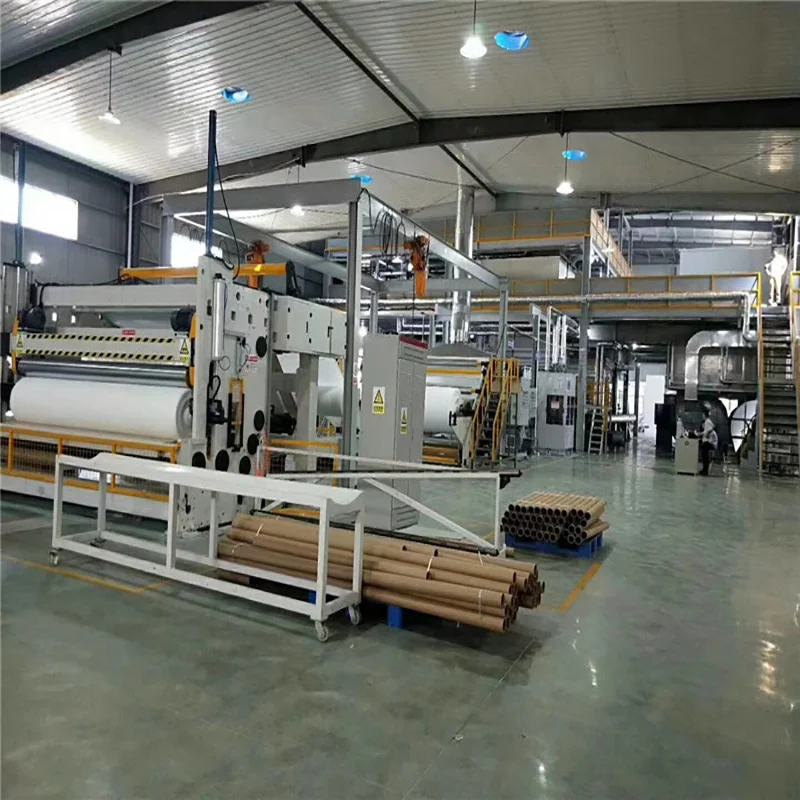
Role of Nonwoven Machinery Manufacturers
The production of melt blown fabric relies heavily on specialized equipment designed by الشركات المصنعة للآلات غير المنسوجة. As leading nonwoven machinery factory in China, we provide quality equipment to oversea market.
Understanding Melt Blown Fabric
Melt blown fabric is a type of nonwoven fabric made from thermoplastic polymers. The process produces very fine fibers, typically less than 10 microns in diameter, which are then collected to form a web-like structure. This fabric is known for its excellent filtration properties, making it ideal for use in masks, مرشحات الهواء, and other applications requiring particulate filtration.
Key Properties of Melt Blown Fabric
- High Filtration Efficiency: The small diameter of the fibers allows for a high surface area, which enhances the fabric’s ability to trap particles.
- Lightweight and Soft: Melt blown fabric is lightweight and has a soft texture, making it comfortable for use in medical applications like face masks.
- Hydrophobic Nature: Many melt blown fabrics exhibit hydrophobic properties, preventing water from penetrating the material, which is crucial for certain applications.
The Melt Blown Fabric Production Process
The production of melt blown fabric involves several key steps:
1. Material Selection
The process begins with the selection of thermoplastic polymers, commonly polypropylene, but also including other materials such as polyester or polyamide. These polymers are chosen based on their desired properties, such as strength, flexibility, and filtration efficiency.
2. Melting the Polymer
The selected polymer pellets are fed into a آلة النسيج المنفوخ الذائب, where they are heated to their melting point. This is typically achieved using a series of heated extruders that continuously feed and melt the pellets. The molten polymer is then transferred to a die.
3. Fiber Formation
Once the polymer is melted, it is forced through a spinneret—a device with multiple small holes—at high pressure. As the molten polymer exits the spinneret, it is subjected to a high-velocity airflow produced by hot air nozzles. This airflow stretches and cools the molten threads, causing them to solidify into fine fibers.
4. Web Formation
The fine fibers produced are collected on a moving conveyor belt or drum. As the fibers cool, they intertwine and form a web-like structure, which is the basis of melt blown fabric. The density and thickness of the fabric can be controlled by adjusting the flow rate of the polymer and the speed of the conveyor.
5. Bonding and Finishing
To enhance the fabric’s properties, the web can undergo additional treatments, such as thermal bonding or the application of adhesive agents. These processes help to improve the fabric’s strength and durability. The finished melt blown fabric can also be treated with anti-static agents or other chemical finishes to enhance its functionality.
6. Cutting and Packaging
Once the melt blown fabric is produced, it is rolled into large sheets or cut into specific dimensions based on its intended application. The final product is then packaged for distribution to manufacturers and suppliers.
Key Equipment Supplied by Manufacturers
- Melt Blown Extruders: These machines are essential for melting and extruding the polymer. They are designed to maintain precise temperature control and provide consistent flow rates.
- Spinnerets: High-quality spinnerets are crucial for producing uniform fibers. Manufacturers offer customizable spinneret designs to meet specific production needs.
- Air Handling Systems: Proper airflow is vital for fiber formation. Nonwoven machinery manufacturers provide air handling systems that ensure optimal airflow and temperature control during production.
- Winding and Cutting Equipment: To prepare the final product, manufacturers supply winding systems that roll the fabric and cutting machines that can slice the fabric into desired sizes.
Innovations in Melt Blown Technology
Nonwoven machinery manufacturers continue to innovate, developing more efficient and sustainable production methods. This includes advancements in automation, which streamline the production process and reduce labor costs. Additionally, manufacturers are focusing on environmentally friendly practices, such as recycling materials and minimizing waste during production.
Applications of Melt Blown Fabric
Melt blown fabric is widely used across various industries due to its unique properties. Some of the most common applications include:
- Medical Supplies: The fabric is primarily used in the production of surgical masks, respirators, and other medical textiles due to its high filtration efficiency.
- Filtration Products: Melt blown fabric is used in air and liquid filters, ensuring the removal of particulates and contaminants in various applications.
- Hygiene Products: This fabric is also used in disposable diapers, feminine hygiene products, and other personal care items.
- Industrial Applications: Melt blown fabric can be utilized in oil absorbents, عازلة, and protective clothing.
Conclusion
The process of manufacturing melt blown fabric is a sophisticated and highly specialized endeavor that plays a vital role in various industries. From its origins in polymer selection to the intricate workings of a melt blown fabric machine, each step is crucial in creating a product known for its exceptional filtration properties and versatility.