The advent of nonwoven fabrics has revolutionized various industries by providing superior alternatives to woven textiles. One pioneering fabrication method essential to many nonwovens is meltblowing, which uses high temperatures and air flows to produce extremely fine fibers. Meltblowing machines precisely control these parameters, outputting consistent products suitable for a diversity of purposes. As nonwovens penetrate more areas, let’s explore the inner workings and utilities of this advanced manufacturing approach.
How Meltblowing Works?
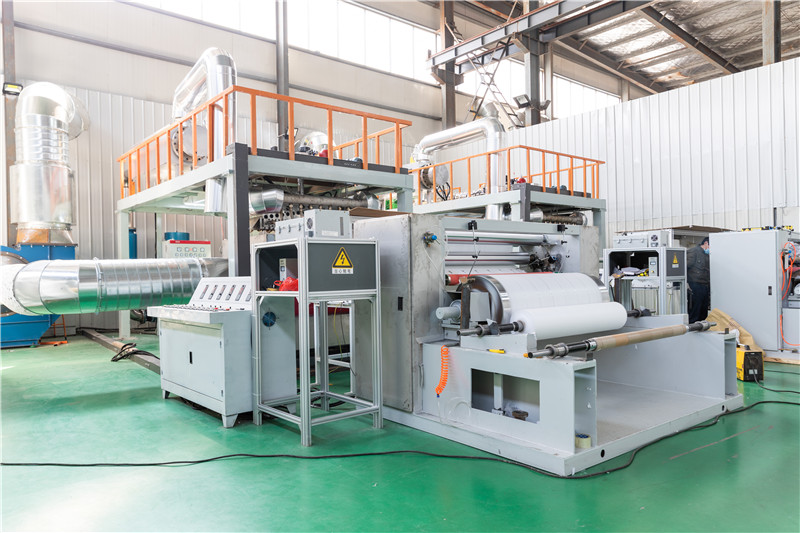
A meltblowing machine by meltblown machine manufacturers, primarily consists of an extruder, spinnerets and air supply system. The extruder melts resin pellets like polypropylene into a liquid state for fiberizing. It then forces the melt through narrow spinneret tips, usually less than 0.5mm in diameter, into a stream of hot high-velocity air. This airstream attenuates the melt into fine fibers around 1 micron in diameter which deposit randomly onto a collector as an integrated web. Auxiliary systems within the machine precisely coordinate all elements.
Fiber Properties and Applications
The extremely small diameters produced through meltblowing give nonwovens good barrier properties while maintaining breathability. This versatility has led to wide commercialization across hygiene, healthcare, filtration and more. Common applications include:
Face masks and other PPE due to ability to capture submicron particulates efficiently.
Diaper topsheets and wipes for softness and liquid management.
Filtration media for air, oil and water purification demanding smaller pore sizes.
Soundproof and thermal insulation fabrics where lightweight loft is prioritized.
Medical fabrics like gowns and drapes needing moisture vapor transmission.
Configuration Flexibility
Meltblowing lends itself well to mass production demands through tailored machine designs. Variables adjustable include number of die slots, die geometry, air temperature and pressure to suit different output volumes and fiber specifications. Integrated calendar rolls further process webs for property enhancements. This tunability customizes fiber morphology to a vast spectrum of performance criteria.
Quality Factors to Consider
Machine features like heated die plates and modular spinneret components maintain thermal uniformity important for consistent fiber formation. Precise temperature and air velocity controls avoid fiber coagulation issues. Robust material feeding components also continually supply uniform melts devoid of contaminants that could compromise web quality or machinery lifespan. Proper filtration and ventilation keep the manufacturing environment clear.
Equipment Scale-Up Complexities
While benchtop-scale prototype meltblowing units suffice for R&D sampling, production demands larger production-worthy machines. However, directly scaling die dimensions presents challenges likes uneven melt distribution which degrades output quality and uniformity. Advanced solutions instead scale-up via multiple die carriage assemblies or tandem/side-by-side configurations maintaining optimized fiber generation parameters. This ensures seamless scaling.
Sustainability Drivers
Minimizing energy usages during meltblowing benefits both cost savings and environmental stewardship goals. Strategies embrace innovative insulation designs, variable speed controlled drives and recapturing thermal energies from exhaust streams using heat exchangers. Biodegradable resin formulations also debut which biofragment after intended use cycles. Combined with optimized processing parameters, sustainability rises significantly across meltblowing operations and downstream value chains.
Constant Technological Refinements
As nonwoven applications proliferate into novel areas, refining meltblowing opens up exciting possibilities. Emerging technologies under investigation include nanofiber meltblowing to access structures beyond current resolution limits. And water-assisted meltblowing shows potential improving fiberization of temperature-sensitive materials. Such advancements along with incorporating renewable resources foretell an even more pervasive role for meltblowing and the nonwovens it enables into the future.