Las máquinas de telas sopladas en fusión producen materiales no tejidos hechos de fibras muy finas formadas mediante un proceso conocido como soplado en fusión.. El proceso de formación de fibras fundidas por soplado., combinado con propiedades como alta superficie y tamaño de poro pequeño, make these nonwovens suitable for a variety of applications.
What Are Melt Blown Fabric Machines?
Melt blown fabric machine – also called melt blowing systems or meltblown lines – consist of several main components:
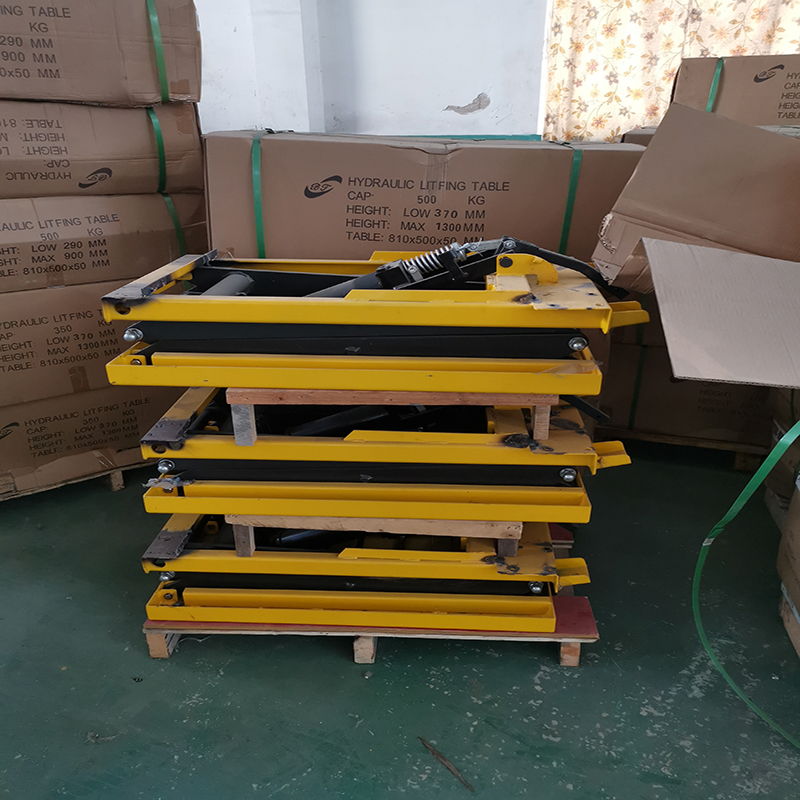
- extrusora – Melts and pumps polymer resins like polypropylene or polyethylene.
- Die assembly – Contains spinnerets or nozzles that extrude the molten polymer.
- Compressed air system – Generates high-velocity air jets that draw out the extruding fibers.
- Cinta transportadora – Collects the extruded fibers to form a nonwoven web.
- Heat and quench section – Solidifies the meltblown fibers.
- Unidad de postratamiento – Includes options for web bonding, slitting and winding.
In operation, molten polymer is extruded through the nozzles while high-speed air jets draw and attenuate the extruding polymer into very fine fibers. The randomly dispersed meltblown fibers are deposited onto a moving conveyor belt, which draws the web at the same rate fibers are being formed.
The web then passes through a heat and quench section that solidifies the fine fiber structure. Post-treatment options bond, consolidate and wind the nonwoven web to produce a useable meltblown fabric.
How Meltblown Fibers Are Formed?
The key aspect of melt blowing is the high-velocity air that exits the die in jets alongside the extruding polymer. As polymer emerges from the nozzles:
- The air stretches and attenuates the nascent fibers very rapidly.
- The fibers are drawn out to fine diameters of 1 micron or less within 20 cm of the die.
- The fiber trajectories become randomized, dispersing fibers uniformly across the web.
The high-temperature air also helps cool and solidify the fibers immediately after formation, stabilizing their thin structure before fibers can recombine.
Features Of Melt Blown Fabric Machines
- Die dimensions – Nozzle width, shape and spacing.
- Air flow – Temperature, pressure and jet velocity.
- Polymer throughputs – How quickly the line converts resin into fabric.
- Web characteristics – Basis weight, espesor, fiber diameter and pore size.
- Line widths – The maximum nonwoven fabric width produced in a single pass.
- Processing capabilities – What polymer types the machine is optimized for.
Manufacturers offer machines with different configurations, throughputs and heating/cooling systems to produce nonwoven webs with varied properties for specific end uses.