Non-woven machines by non woven machine manufacturers, are essential equipment in the production of non-woven fabrics, catering to diverse industries and applications. Understanding the different types, working principles, and applications of these machines is crucial for selecting the right machine that aligns with your specific production requirements.
Types of Non-Woven Machines:
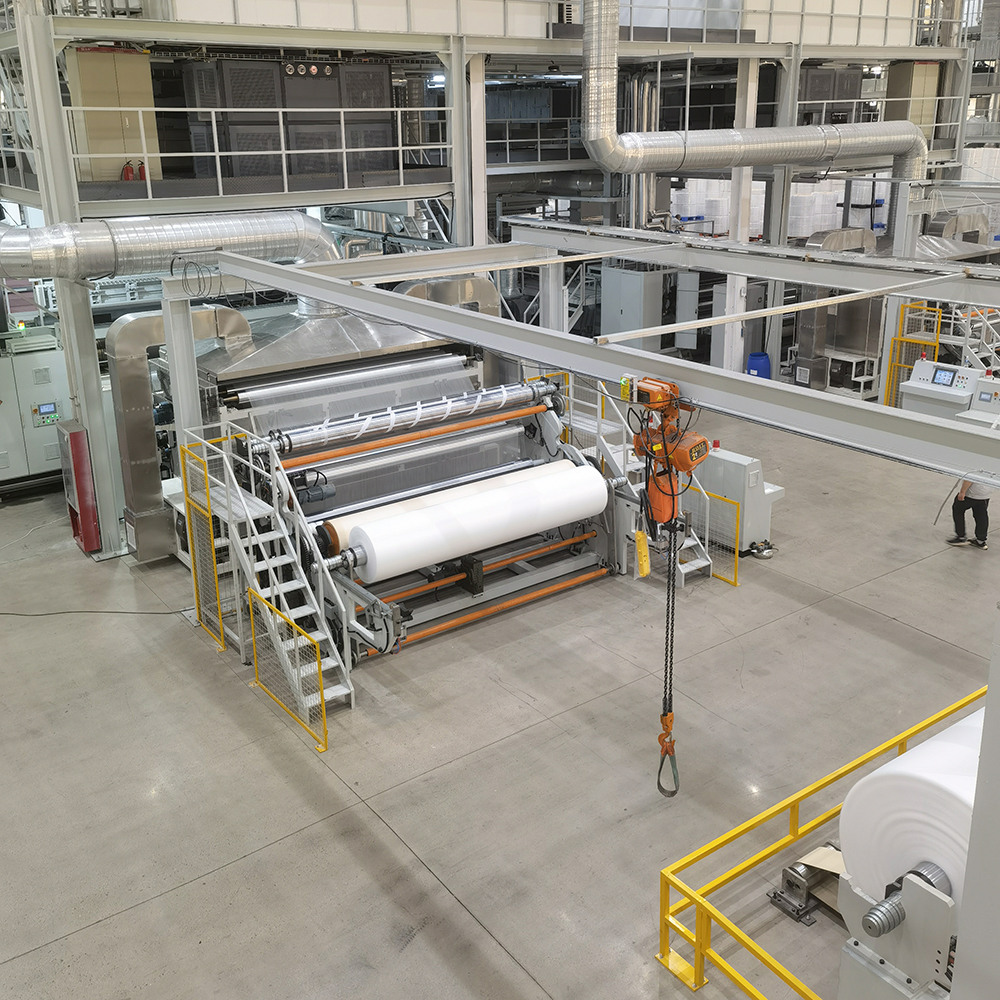
Carding Machines: Carding machines mechanically align and disentangle fibers, creating a uniform web of fibers that serves as the base for non-woven fabrics.
Air-Laying Machines: Air-laying machines utilize air currents to deposit fibers onto a conveyor belt, forming a non-woven web with a fluffy texture.
Wet-Laying Machines: Wet-laying machines disperse fibers in a water suspension, which is then dewatered to create a non-woven web with high strength and density.
Melt-Blowing Machines: Melt-blowing machines extrude molten polymers through tiny nozzles, creating fine fibers that are collected to form a non-woven web.
Spunbond Machines: Spunbond machines combine spinning and bonding processes, producing continuous filaments that are directly bonded to form a non-woven web.
Working Principles of Non-Woven Machines:
Carding: Carding machines use rotating rollers covered with wire brushes to align and separate fibers, removing impurities and creating a uniform fiber web.
Air-Laying: Air-laying machines generate a stream of air that carries fibers onto a moving conveyor belt. The fibers are deposited in a random pattern, resulting in a soft and bulky non-woven web.
Wet-Laying: Wet-laying machines mix fibers with water to create a slurry, which is then spread onto a conveyor belt. The water is removed through dewatering processes, leaving behind a dense and strong non-woven web.
Melt-Blowing: Melt-blowing machines melt polymers and extrude them through tiny nozzles, creating a stream of fine fibers. These fibers are collected on a moving conveyor belt, forming a non-woven web with excellent filtration properties.
Spunbond: Spunbond machines combine spinning and bonding processes. Polymer resins are melted and extruded through spinnerets, forming continuous filaments. These filaments are then directly bonded to each other, creating a strong and durable non-woven web.
Applications of Non-Woven Fabrics:
Medical and Hygiene Products: Non-woven fabrics are extensively used in the production of disposable medical gowns, surgical masks, bandages, and hygiene wipes.
Automotive Industry: Non-woven fabrics are employed in car interiors as headliners, seat covers, and sound insulation materials.
Filtration and Packaging: Non-woven fabrics are used in air and liquid filtration systems, as well as in packaging materials such as tea bags and coffee filters.
Geotextiles: Non-woven fabrics are utilized in civil engineering applications such as soil stabilization, erosion control, and drainage systems.
Home Furnishings: Non-woven fabrics are found in various home furnishing products, including carpets, curtains, and upholstery.
Factors to Consider When Selecting a Non-Woven Machine:
Production Capacity: Determine the desired output capacity of the machine based on your production requirements and market demand.
Fabric Type: Consider the type of non-woven fabric you intend to produce, as different machines are suitable for specific fabric structures and properties.
Raw Material: Evaluate the compatibility of the machine with your chosen raw materials, whether they are natural fibers, synthetic fibers, or blends.
Automation Level: Choose between manual, semi-automatic, or fully automatic machines based on your production scale and budget.
Energy Efficiency: Consider the energy consumption of the machine and its impact on your operating costs.
Maintenance and Support: Ensure that the machine comes with proper maintenance guidelines and readily available support from the manufacturer or supplier.