Melt blowing technology precisely forms nonwoven fabrics possessing extremely fine fiber diameters and a variety of productive applications. Sophisticated machinery lies at the heart of this specialized manufacturing process.
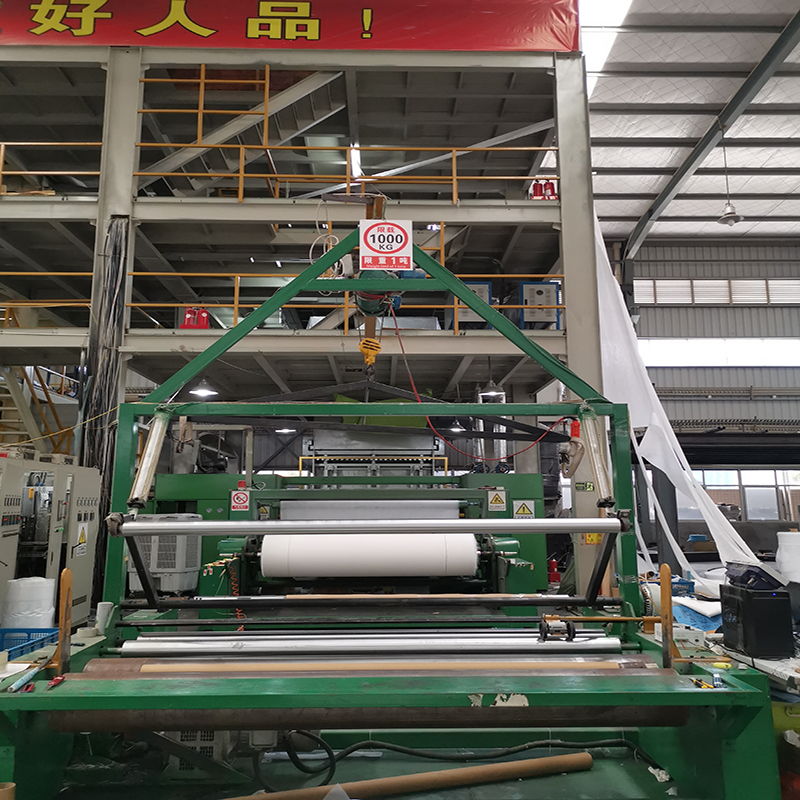
How it Works
Thermoplastic resin pellets are melted and extruded through microscopic die openings, forming continuous streams of molten material. High-velocity hot air flows split and attenuate the filaments as they exit, drawing them into micro-thin fibers between 0.1-10 microns in diameter. The airstreams convey fibers onto a moving belt where they collide, entangle and form a unified web. Deposited fibers cool and solidify, resulting in a uniform nonwoven sheet.
Machine Design
Precise die engineering determines fiber size and web properties. Small variances impact filtration efficiency or texture. Dies heat plastics evenly to controlled melt temperatures without decomposition. Multi-orifice designs maximize throughput. Air knife assemblies precisely regulate pressures and velocities stabilizing filaments. Specially coated collectors uniformly consolidate webs. Industrial-grade frames, bearings and motors withstand intensive operation. Programmable logic controls optimize running parameters.
Processing Flexibility
Adjustable process variables tailor webs for end uses. Altering air velocity/temperature and resin type influences fiber morphology, basis weight, pore structure and mechanical properties. Bi-component configurations core a lower-melting skin around a higher-melting core for specific effects. Continuous rolling production accepts an array of feedstock types suited to varied filtration or absorption applications.
Quality is Paramount
Precise fiber microstructure dictates performance, so quality control remains critical. Online monitoring detects deviations in line speed, air pressures, fiber diameter or web uniformity for swift adjustments. Post-line testing evaluates properties like pore size, static charge, strength and permeability. Strict changeover procedures minimize contamination when switching resin types or winding bulk continuous rolls in clean room environments.
Engineering Excellence
Leading machinery OEMs conduct extensive R&D optimizing designs, crucially in areas like die tips featuring advanced surface modifications extending service life under corrosive processing conditions and minimizing waste. They establish global reputations through process expertise delivering consistent, validated products fulfilling the most stringent industrial standards. Thoughtful automation and ergonomic designs maximize uptime safely meeting bulk production demands cost-effectively.
In Conclusion
Specialized máquina de tela soplada por fusión lies at the core of manufacturing superior nonwoven fabrics supporting industries from healthcare and HVAC to geosynthetics and beyond. Continued engineering progress ensures this technology sustainably produces filtration media and materials helping global populations for decades to come.