Spunbond nonwovens are manufactured using a continuous spunbond process line consisting of spunbond nonwoven fabric make machines. The production technology involves extruding thermoplastic polymer filaments which are then laid onto a conveyor belt to form a web. Let’s take a closer look at the key parts of a typical spunbond nonwovens production line.
Main 5 Methods To Produce By Spunbond Nonwovens Production Line
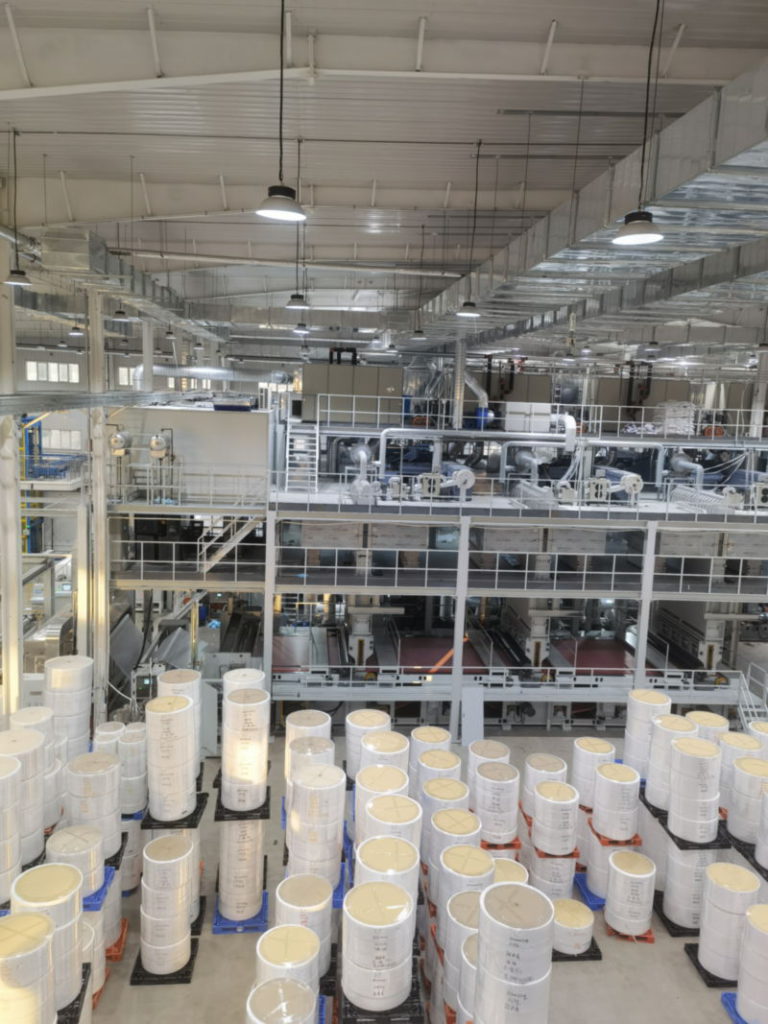
- Pezón hilador: The polymer resin in pellet or granule form is melted and filtered before being extruded through the spinnerets. The spinnerets have many tiny holes through which the molten polymer is extruded to form continuous filaments.
- Pulling section: The freshly extruded filaments are pulled and drawn down by a series of pullers and godet rolls at high speeds to reduce the diameter and orient the polymer chains. Air knives help cool and flatten the filaments.
- Laydown section: The drawn filaments are deposited in a random manner onto a moving belt by means of an air-jet delivery system. This forms a nonwoven web. Additional spinnerets and laydown systems allow production of multicomponent or laminated webs.
- Bonded section: The deposited web then passes through an oven or underneath an array of heat sources which melts and fuses the filaments together at points of contact. This bonds the web.
- Winder: The finished spunbond nonwoven fabric web is wound onto a roll by collapse and winder drums before being sent for slitting and cutting.
Introduce About Key Spunbond Nonwoven Fabric Make Machine Components
The key spunbond nonwoven fabric make machine components – the extrusion system, pulling section, laydown system and bonder – work together in an integrated línea de producción de telas no tejidas hiladas to manufacture the end product. Continuous production and high line speeds allow for mass manufacturing of spunbond nonwovens.
The Most Common Applications Of Spunbond Non-wovens
- En primer lugar, spunbond nonwovens are widely used to manufacture wipes for household, baby, medical and industrial cleaning due to their strength, durability and absorbency.
- Secondly, spunbond nonwovens are used as separators, reinforcement fabrics and filters in geotechnical applications like road construction, drainage layers and erosion control due to their durability, porosity and water permeability.
- Thirdly, spunbond fabrics are commonly used as filter media for air, liquid and gas filtration in applications like HVAC filters, máscaras faciales, automotive filters etc.