A spunmelt nonwoven machine as used to produce various nonwoven materials including hygiene products, filtration media, and apparel fabrics. A common type of spunmelt machine is the polypropylene (ПП) single-step sandwich meltblown spunmelt machine (ССММС), which produces combined spunbond and meltblown webs in a single process. This ПП SSMMS центрифугирующая машина offer high performance and yield for nonwoven manufacturers.
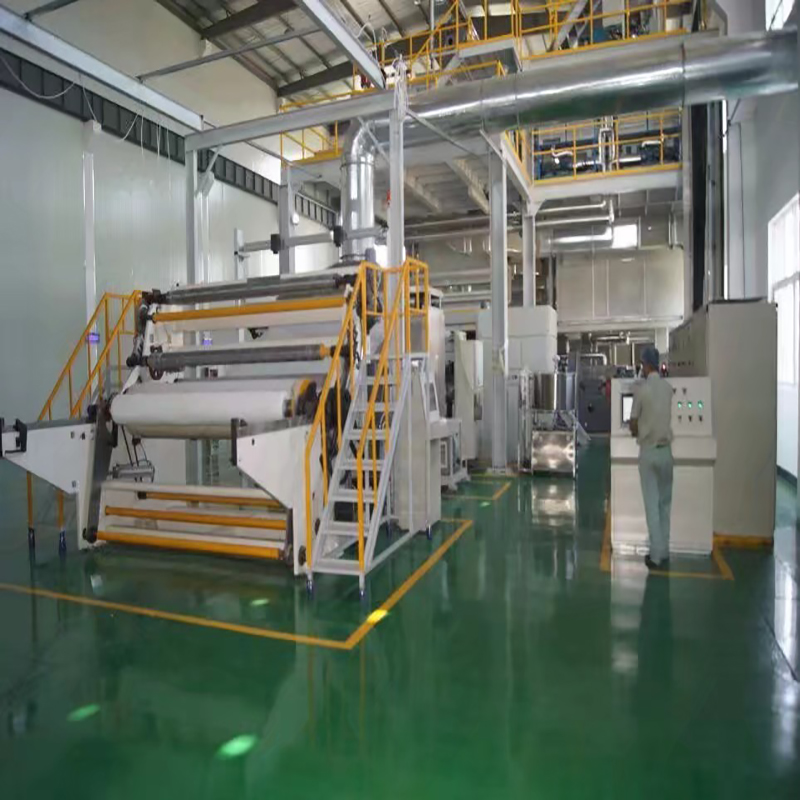
Introduce about PP SSMMS spunmelt machine
In a PP SSMMS spunmelt machine, polymer granules like polypropylene are first fed into a hopper and conveyed into the extruder. Inside the extruder, the polymers are melted and forced through a spinneret. The spinneret contains many tiny holes that create continuous polymer filaments as they exit.
As the molten filaments exit the spinneret, they are drawn vertically by a godet system where they are cooled by air. As the filaments harden, they become thinner and more stable, forming continuous fibers. These fibers then pass through the sandwiching area where hot air to form the meltblown layer is injected in between the spunbond layers.
The sandwiching area is a key feature of single-step SSMMS machines. In this section, the spunbond fibers pass between an upper and lower conveyor, with hot air blown from nozzles in between to create the meltblown layer. The amount of hot air, air pressure and nozzle arrangement determine the basis weight and thickness of the meltblown layer.
After sandwiching, the combined web consisting of spunbond and meltblown layers passes over a roller bed and into an oven for annealing and further cooling. The annealed composite web is then wound onto a take-up roller.
The key advantages of PP SSMMS machines include:
- High production rates – Up to 800 kg/hr of nonwoven material can be produced.
- Width flexibility – Web widths from 1.2 к 4.5 meters are possible, depending on the machine.
- Better control of layer ratios – The combination ratio of spunbond to meltblown layers
can be precisely set from 20/80 к 80/20. - Uniform web weights – Precise control of spinning, air flow and winding ensure consistent
basis weights within +/- 3%. - Superior quality and performance – The integrated process produces composite webs with
bonding between layers for improved strength, barrier properties and filtration.
PP SSMMS machines also require less space and capital investment compared to traditional two-step systems that produce spunbond and meltblown layers separately and laminate them later. Однако, the single-step process does involve more complex control of the sandwiching section.
When selecting a PP SSMMS spunmelt machine, manufacturers should consider factors like web width, production rate, layer ratio flexibility, Energy efficiency, technical support and maintenance requirements. Machine suppliers often offer custom configurations and options to meet the specific application needs for products like diapers, wipes, filters and geotextiles.