In the realm of textiles, nonwoven fabrics have carved out a significant niche due to their unique properties and versatile applications. Among the various methods of producing nonwoven fabrics, meltblown technology stands out, particularly for its ability to create high-performance materials. This blog post will delve into meltblown machines, their significance in nonwoven fabric production, and the broader landscape of nonwoven fabric machinery.
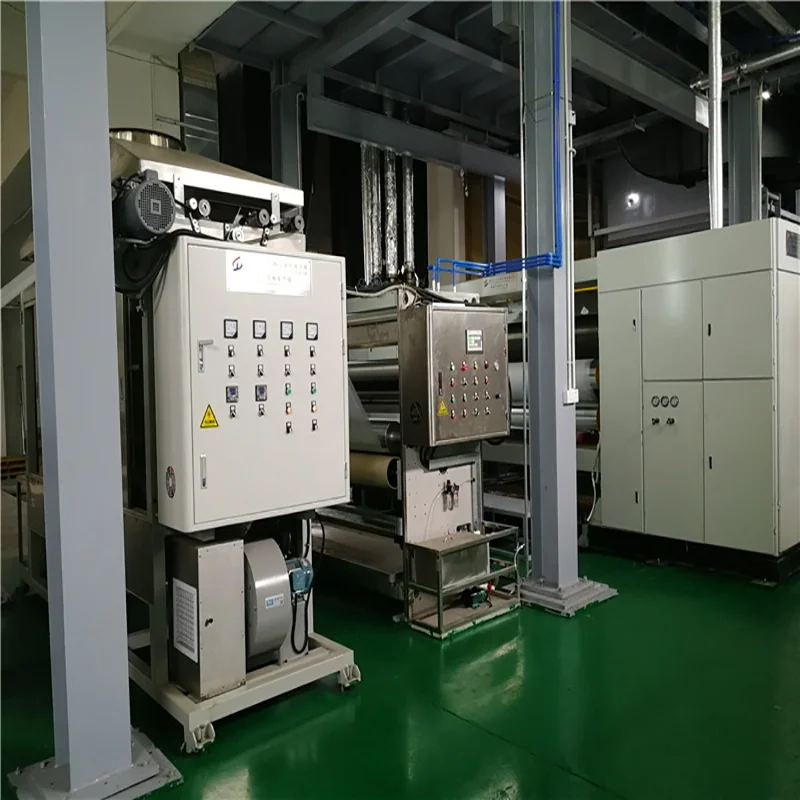
What is Meltblown Nonwoven Fabric?
Meltblown machine nonwoven fabric is produced by extruding molten polymer through fine nozzles, creating microfibers that are blown onto a conveyor belt. These fibers intertwine to form a web, which can be further processed to enhance its properties. Meltblown fabrics are known for their high filtration efficiency, making them ideal for applications such as medical masks, air filters, and insulation materials.
Key Characteristics of Meltblown Nonwoven Fabric
- Fine Fiber Structure: The meltblown process produces extremely fine fibers, often less than one micron in diameter. This results in a dense fabric with excellent filtration capabilities.
- High Absorbency: Meltblown nonwoven fabrics can absorb liquids effectively, making them suitable for hygiene products like absorbent pads and medical gowns.
- Lightweight and Soft: Despite their strength, meltblown fabrics are lightweight and soft to the touch, enhancing comfort in applications such as apparel and personal protective equipment (PPE).
The Meltblown Machine: An Overview
A meltblown machine is specialized equipment designed to produce meltblown nonwoven fabric. These machines consist of several key components that work in harmony to create high-quality fabric.
1. Extruder
The extruder is the heart of the meltblown machine, where raw polymer pellets are melted and converted into a molten state. The temperature and pressure within the extruder are carefully controlled to ensure consistent polymer flow.
2. Spinneret
The spinneret is a crucial part of the meltblown machine, featuring numerous tiny nozzles through which the molten polymer is extruded. The design of the spinneret can significantly affect the fiber diameter and distribution.
3. Air Blower
Once the fibers are extruded, a high-velocity air stream from the air blower is used to draw and stretch the fibers. This process not only creates fine fibers but also helps to lay them down onto a moving conveyor belt.
4. Conveyor Belt
The conveyor belt collects the laid fibers, allowing them to bond together to form a nonwoven fabric. Depending on the desired end product, the fabric can be further processed through additional steps such as thermal bonding or chemical treatments.
5. Winding Unit
After the fabric is formed, it is wound onto rolls for storage and distribution. The winding unit is essential for ensuring that the final product is ready for subsequent processing or shipping.
Applications of Meltblown Nonwoven Fabric
Meltblown nonwoven fabrics have found a wide range of applications across various industries:
1. Medical and Hygiene Products
One of the most significant uses of meltblown nonwoven fabrics is in medical and hygiene products. From surgical masks and gowns to absorbent pads and diapers, meltblown fabrics provide essential barrier protection and fluid management.
2. Filtration
Due to their high filtration efficiency, meltblown fabrics are widely used in air and liquid filtration applications. They are commonly found in HVAC systems, automotive filters, and water purification systems.
3. Insulation
Meltblown nonwoven fabrics are also utilized in insulation materials for construction. Their lightweight and thermal resistance properties make them effective in maintaining energy efficiency in buildings.
4. Geotextiles
In civil engineering, meltblown fabrics are used as geotextiles to enhance soil stability and erosion control. Their permeability allows water to pass through while providing structural support.
The Importance of Nonwoven Fabric Machines
Beyond meltblown technology, the broader category of non woven fabric machines plays a critical role in the textile industry. These machines encompass various processes, including spunbond, needle punching, and hydroentangling.
1. Spunbond Technology
Spunbond machines create nonwoven fabrics by extruding continuous filaments that are laid down in a web formation. This method is known for producing strong and durable fabrics, often used in applications like agricultural covers, hygiene products, and automotive interiors.
2. Needle Punching
Needle punching machines use barbed needles to interlock fibers, creating a dense, felt-like fabric. This technology is commonly employed in automotive carpets, insulation, and geotextiles.
3. Hydroentangling
Hydroentangling machines use high-pressure water jets to entangle fibers, resulting in a soft and absorbent fabric. This method is often used for producing wipes, medical textiles, and personal care products.
The Future of Nonwoven Fabric Machinery
As industries evolve and demand for innovative materials increases, the future of nonwoven fabric machinery looks promising. Advances in automation, digitalization, and eco-friendly practices are set to enhance production efficiency and sustainability.
1. Automation and Smart Technology
The integration of smart technology and automation in nonwoven fabric machines is transforming production processes. Real-time monitoring and data analytics can optimize machine performance, reduce downtime, and improve product quality.
2. Sustainable Practices
With growing environmental concerns, manufacturers are increasingly focusing on sustainability. Nonwoven fabric machines that utilize recycled materials or produce biodegradable fabrics are gaining popularity.
3. Customization and Flexibility
The ability to customize nonwoven fabric production to meet specific market needs is becoming vital. Machines that allow for quick changes in production settings will enable manufacturers to respond swiftly to evolving consumer demands.