Meltblown nonwoven fabric is made using a meltblown machine that extrudes specialized thermoplastic polymers through tiny nozzles to produce extremely fine fibers. These meltblown fibers are randomly deposited and bonded together to create an insulating material with many unique properties.
Meltblown Machine Nonwoven Fabric
A meltblown machine uses high-velocity air to draw and attenuate extruded thermoplastic material into fine fibers with diameters typically between 0.5 to 15 microns. The fine fibers are randomly deposited on a forming surface to create a web of entangled fibers that constitutes the nonwoven fabric.
Meltblown nonwoven fabric is widely used as a filter or barrier material due to its small fiber structure, high surface area, and porosity. It is commonly made from polymers like polypropylene and polyester.
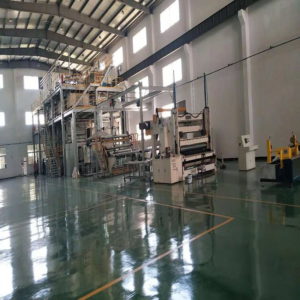
Nonwoven Fabric Produce By Meltblown Make Machine
The meltblown process can produce webs with basis weights between 5 to 300+ gsm through melt blown machine. Actually, It depends on the production settings and end use of the nonwoven material. Fabric properties like density, pore size distribution, stiffness and tensile strength are determined by factors like the polymer used, extrusion temperature, air flow, throughput rate and more.
A meltblown make machine or line consists of several components:
- An extruder to melt and feed the thermoplastic material
- Slot die nozzles that extrude the molten polymer
- High-temperature heated air blowers that draw and attenuate the extruded material into fibers
- A forming surface where the fibers are collected
- A collection bed and winding system
- An oven or treatment unit to thermally bond the fibers together
- Various rolls and tensioners to control the web movement
4 Key Challenges In Producing High-quality Meltblown Nonwovens Fabric
- The meltblowing process needs to extrude the polymer at a precise and uniform rate to achieve consistent fiber diameter and basis weight. Any fluctuations can cause nonuniformity in the resulting fabric.
- The fiber diameter has a major influence on fabric properties like pore size and density. Precisely controlling the air flow and extrusion variables is required to maintain a narrow fiber diameter distribution.
- Short bursts of thicker fibers, known as “shot noise”, can occur sporadically during meltblowing. This creates areas of nonuniform basis weight and needs to be minimized.
- The small nozzles in the die head are prone to clogging, especially with fillers and additives in the polymer. Frequent cleaning and monitoring is required to maintain consistent fiber formation