The PP (Polypropylene) melt blown machine has emerged as a critical component in the manufacturing landscape, particularly within the nonwoven fabric industry. It is an innovative and specialized piece of equipment that utilizes advanced technology to transform polypropylene pellets into ultrafine fibers, which are then used to create a variety of essential products, most notably in filtration media for face masks, air filters, and other hygiene and medical applications.
Understanding the PP Melt Blown Process
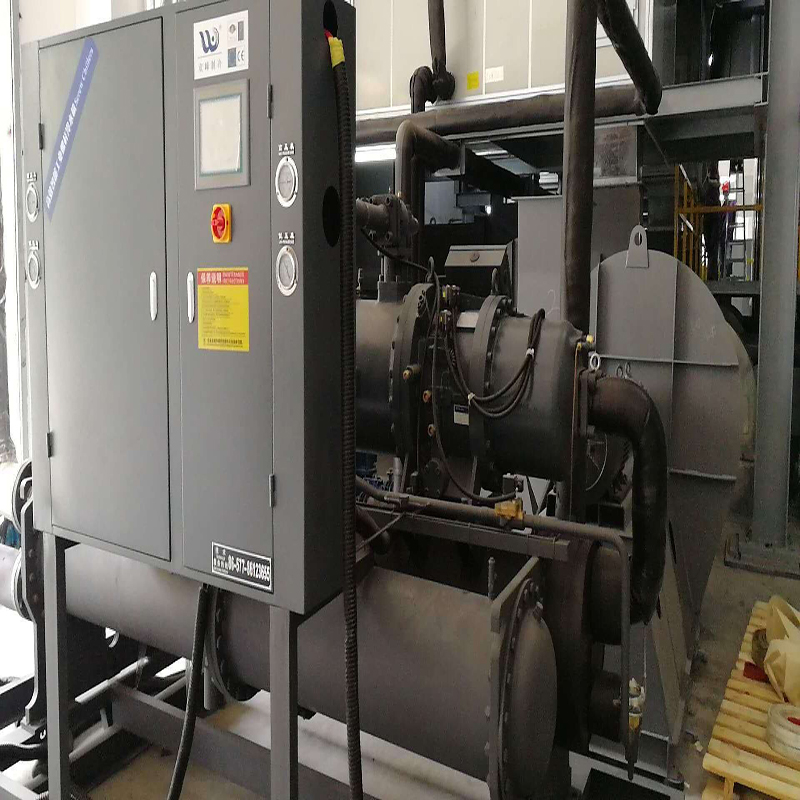
At its core, the PP melt blown process involves melting polypropylene resin pellets at high temperatures until they reach a molten state. This liquid polymer is then extruded through tiny die nozzles using high-pressure air streams. These jets of hot air stretch and thin the molten polymer into microfibers, which cool and solidify almost instantly upon contact with ambient air. The resulting web of randomly oriented fibers is collected on a moving belt or roller, forming a nonwoven fabric.
A typical PP melt blown machine consists of several key components:
1.Extruder: This is where the polypropylene pellets are heated and melted to form a continuous viscous stream.
2. Die Head: Equipped with numerous small holes, this part disperses the molten polymer into fine filaments under high pressure.
3. Air System: Comprising heaters and blowers, it provides the high-velocity hot air necessary to attenuate and disperse the fibers.
4.Collection Belt/Drum: This is where the formed nonwoven fabric collects after being blown by the air system.
5.Winding Unit: After the material has been cooled and solidified, it is wound onto rolls for further processing or conversion into final products.
PP melt blown nonwovens have found widespread use due to their unique properties such as high porosity, low density, and excellent filtration capabilities. Some primary applications include:
Medical & Health Care: The COVID-19 pandemic has highlighted the importance of PP meltblown nonwovens as the critical middle layer in surgical and N95 respirator masks, providing exceptional particle filtration.
Filtration Industry: They serve as efficient filter media for air conditioning systems, vacuum cleaners, and industrial air pollution control systems.
Hygiene Products: They are utilized in absorbent cores for baby diapers, feminine hygiene products, and adult incontinence products due to their liquid absorption and retention abilities.
Electronics & Insulation: They offer thermal and acoustic insulation, as well as EMI shielding in electronic devices.
Technological Advancements and Challenges
As demand for high-quality filtration materials grows, so does the need for improved melt-blown technology. Manufacturers are continually striving to enhance production efficiency, reduce fiber diameter to increase filtration performance, and optimize energy consumption. However, challenges remain, including maintaining consistent fiber quality, reducing waste, and scaling up production while keeping costs manageable.
PP melt blown machine stands as a testament to the ingenuity and advancements in material science. Its pivotal role in producing nonwoven fabrics that protect human health and improve the functionality of various consumer and industrial goods underscores its significance in today’s world. As research and development continue, we can anticipate even more innovative uses for these machines and the versatile materials they produce.